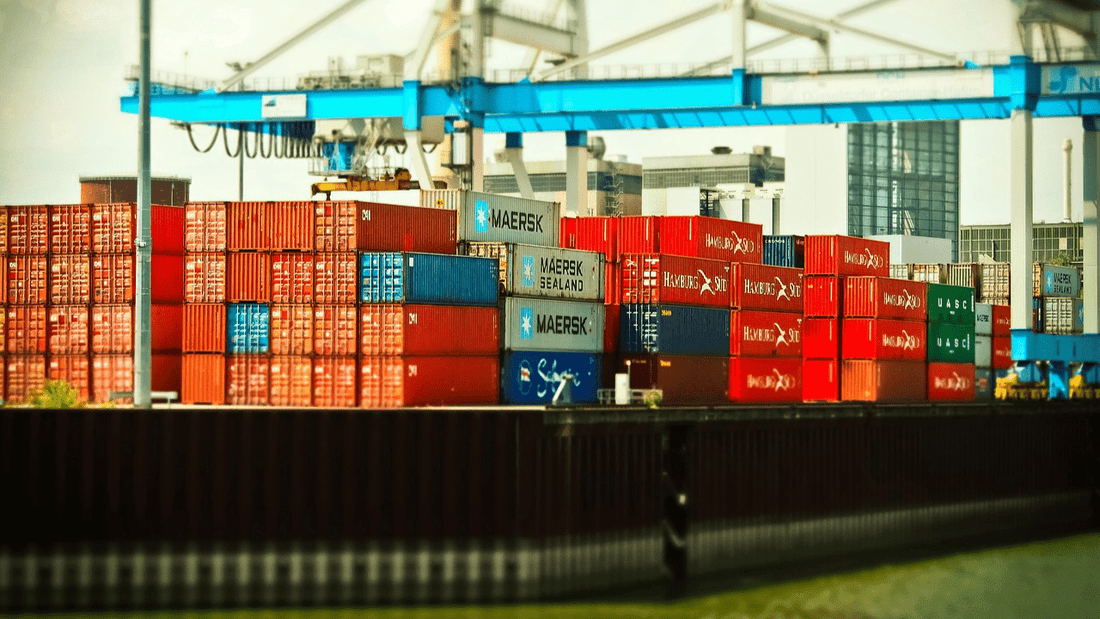
How Shipping Containers Are Loaded Onto Cargo Ships
Share
Global trade depends on a system that’s as complex as it is efficient. At the center of that system are shipping containers—and the method used to load them onto cargo ships is a highly coordinated operation that blends machinery, logistics, and human expertise. While it may seem straightforward on the surface, the process of getting thousands of shipping containers onto one vessel is anything but simple.
Here’s a closer look at how it all comes together:
It Starts at the Container Terminal
Before a shipping container reaches the deck of a cargo ship, it arrives at the terminal—typically by truck or rail. There, it undergoes a series of check-in procedures: documentation is verified, identification tags are scanned, and the container is directed to a specific storage location within the terminal yard.
These yards are carefully mapped out using digital planning systems. Each container is assigned a temporary slot based on multiple factors: weight, destination, cargo type, and when it’s scheduled to be loaded. This digital infrastructure is essential for keeping track of thousands of containers and ensuring they are loaded in the correct order.
Planning the Load: The Stowage Strategy
The next phase in the process is stowage planning. Cargo ships don’t get loaded randomly; they follow a detailed “stow plan” that dictates the exact placement of each shipping container. This plan is built to ensure the ship remains stable, structurally balanced, and efficient at every port of call.
Shipping containers bound for earlier stops are loaded last so they can be offloaded quickly. Heavier units go on the bottom, with lighter ones stacked above. Hazardous or temperature-sensitive cargo is handled according to strict international regulations. All of this planning helps reduce time in port and minimizes the risk of delays or cargo damage at sea.
Lifting with Precision: The Role of Ship-to-Shore Cranes
Once loading begins, massive ship-to-shore cranes take over. These towering machines are designed to lift shipping containers from the dock and position them with pinpoint accuracy aboard the vessel. Most operate on rails that run along the edge of the quay, moving back and forth in coordination with the ship’s position.
Each crane is equipped with a spreader—a locking mechanism that attaches securely to the corners of a shipping container. Once the spreader locks in place, the crane lifts the container, swings it out over the ship, and gently lowers it into its assigned spot. Despite the enormous size and weight of each container, this process is remarkably controlled.
Cranes may be operated manually by personnel in elevated cabins, or remotely from nearby control centers. In more advanced ports, automation is increasingly playing a role, with systems using sensors and software to position containers more quickly and safely.
Securing the Load
After a shipping container is placed, it must be secured. Longshoremen fasten each container using devices like twist locks, turnbuckles, and lashing rods. This is critical for safety—once at sea, ships can encounter severe weather, and containers must remain stable through swells and wind.
Securing the containers is physically demanding work that still relies heavily on human labor. Teams move quickly between rows, locking each shipping container to the one beneath it and anchoring the stack to the ship’s deck or hold. Depending on the ship’s design, containers may be stacked eight or nine high above deck, with additional rows packed below.
Time is Money: Working Against the Clock
Time is always a factor. The world's busiest ports operate around the clock, with multiple cranes working simultaneously to load and unload thousands of shipping containers in as little as 12 to 24 hours. The faster a ship can be turned around, the more efficient and profitable the route becomes.
To keep everything on schedule, logistics teams monitor the loading process in real time, ready to make adjustments if a container is delayed or a crane experiences a mechanical issue. Efficiency depends on constant communication between the ship's crew, crane operators, terminal staff, and logistics coordinators.
Special Considerations for Unique Cargo
Not all shipping containers are the same. Refrigerated containers—known as reefers—require immediate access to power sources once on board, which means they must be loaded in specific locations with electrical connections. Out-of-gauge cargo, such as oversized machinery or vehicles on flat racks, must be carefully placed and secured using specialized procedures.
Dangerous goods are also subject to tight regulations. These containers are isolated in designated areas and clearly marked for safety and compliance. All of these considerations are built into the stow plan before loading even begins.
Technology Behind the Scenes
Much of what keeps the operation moving efficiently happens behind the scenes. Terminal operating systems (TOS), real-time tracking software, and automated yard equipment are critical in managing container flow. RFID tags and GPS help track each container’s exact location, both on land and at sea.
Ports are increasingly adopting digital twins—virtual models of the terminal environment—to simulate operations and reduce congestion. As global demand grows, this kind of smart infrastructure helps ports handle more cargo without expanding physically.
The Big Picture
While the physical act of lifting and placing shipping containers is impressive in itself, the broader achievement lies in the coordination. Every container loaded onto a ship represents a carefully timed step in a global supply chain. It involves rail schedules, trucking routes, customs clearance, digital planning tools, and international regulations—all aligned to make sure goods arrive on time and intact.
Fill out the form below for a free shipping container quote from USA Containers: